FASTENERS FOR
SPECIAL MATERIALS
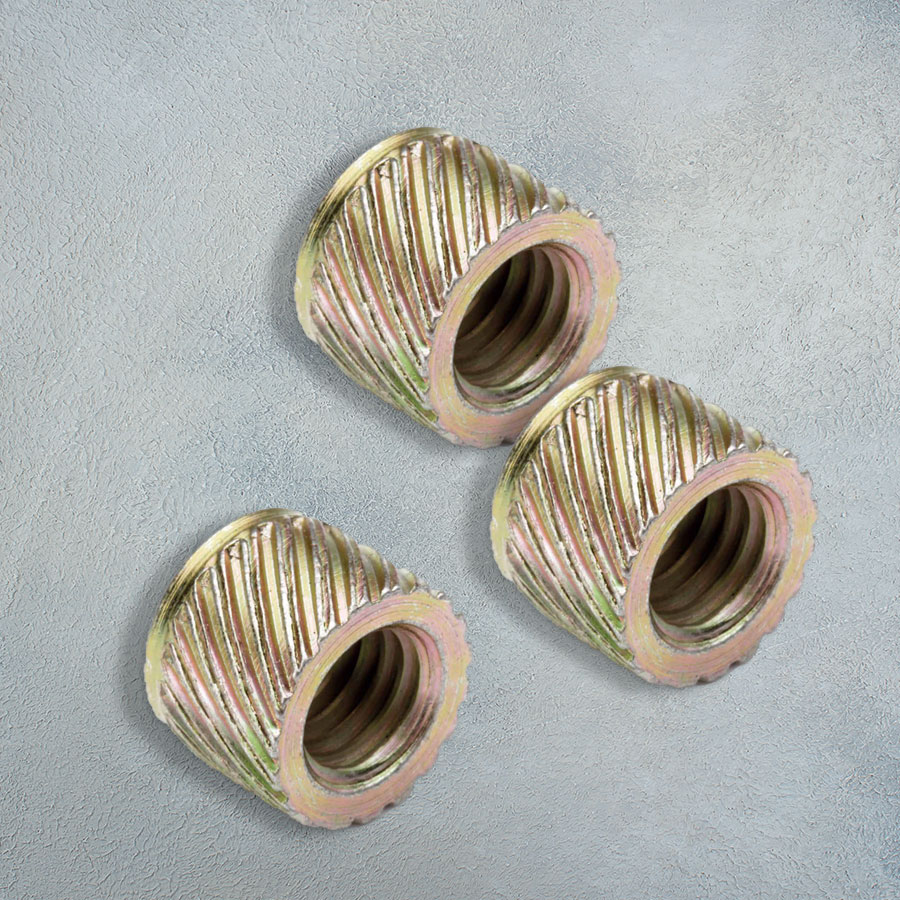
Introduction
The introduction of new materials and their successful use by designers are usually dependant on a mechanical fastening system
to allow dismantling for adjustment, servicing or repair.
The captive fasteners shown in this catalogue have been designed to meet the needs of designers who require the strength of a steel thread when using lightweight alloys such as magnesium and resin based printed circuit boards.
The information in this catalogue is intended as a general guide.
For further advice please consult your local PSM Sales Engineer or our Applications Engineers at info@rgafasteners-psm.com, alternatively you can fill out our Online Quotation Form. The PSM Technology Centre can also provide pre-production test facilities for accurate performance data.

PRECISION HARDENED INSERTS & STUDS
These fasteners have been designed to provide a hardened steel thread to resist tensile and torsional loading in the softer aluminium and zinc based diecastings.

HARDENED STEEL SCREW-SERTS
The Screwsert range of fasteners have been designed to provide a hardened steel thread in the softer aluminium and zinc based diecastings, magnesium and thermosetting plastics.
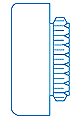
PRINTED CIRCUIT BOARD FASTENERS
These fasteners have been designed to provide a metallic deep tapped thread into resin based printed circuit boards.
PRECISION HARDENED INSERTS & STUDS
Precision hardened inserts & studs have been designed to provide a hardened steel thread to resist tensile and torsional loading in the softer aluminium and zinc based diecastings.
The external spiral knurl cuts into the parent material reducing radial stresses in the casting.
ADVANTAGES
- Easy assembly with any squeeze press
- Low bursting stress allows the use of thinner walled bosses
- Steel thread provices a high degree of re-usability
- Installed into plain cored hole
- Eliminates tapping operations
DESIGN GUIDE
JOINT DESIGN
To achieve optimum pull-out performance the joint must be designed with a stationary mating component in contact with the face of the insert.
HOLE PREPARATION
Holes may be cored or drilled. The taper on a cored hole should be 0.5~ inclusive and the hole diameter recommended should apply at the point reached bythe bottom of the insert.
INSTALLATION
See page 8.
WALL THICKNESS
The minimum wall thickness will vary with the ductility of the diecasting alloy, but as a general guide wall thickness should not be less than the nominal thread diameter.
Specific use of materials like magnesium and applications requiring thinner boss walls may require subtle changes to the design of the insert. In either case consultation with the PSM Technology Centre or local Sales Office and pre-production testing is essential.
For More Information
Contact Us
For More Information
Quotation Form
Fill out our Online Quotation Form
For More Information
Account Application
Fill out & email or fax back